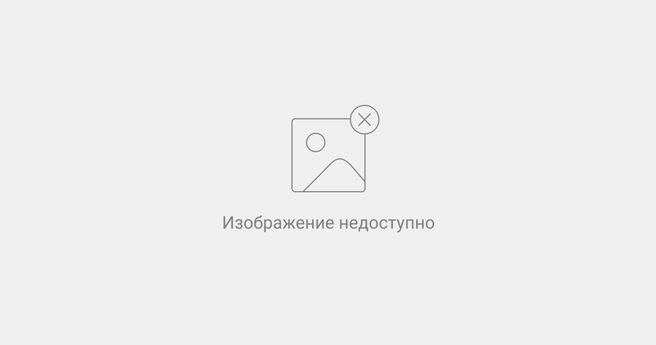
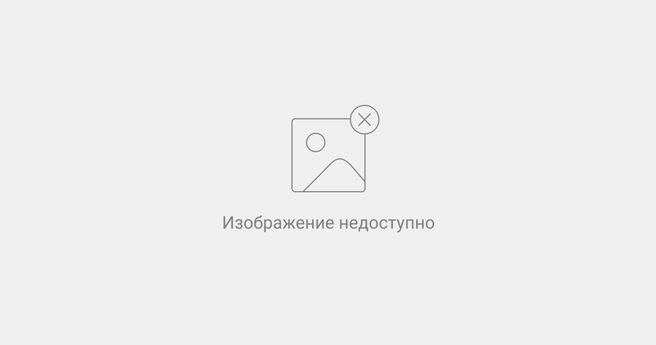
На этом самом месте 50 лет назад кипело производство «Волги» ГАЗ-21, а теперь полное впечатление, будто на эту 31 тысячу квадратных метров телепортировался кусочек Европы – до того не по-нашему, не по-советски смотрится кузовной цех изнутри. Расторопные роботы, заморские надписи и освещенность, как в оранжерее.
Концерн Volkswagen приехал сюда, так сказать, со своей «мебелью», и российский вклад выдают разве что логотипы «Группы ГАЗ» на спецовках рабочих, да редкие-редкие приборы, оставшиеся со старых времен – на них даже шрифты советские, рукописные.
На улице «памятников истории» больше, особенно трогает «Спасибо за добросовестный труд!» на выходе с главной проходной. Вот только на совесть рабочих больше не уповают – нынче за качество отвечает система аудита.
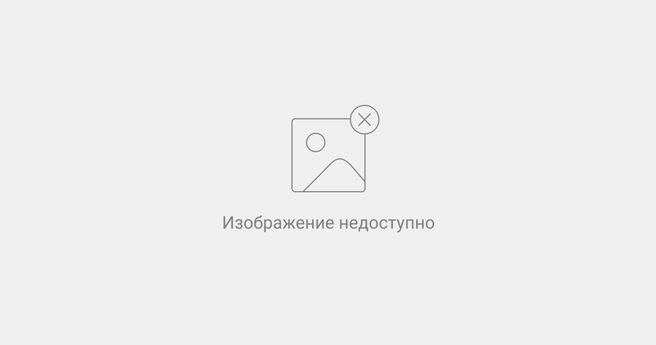
К лету завод будет производить три модели – Skoda Yeti, VW Jetta и новую Skoda Octavia
А что это там правят деревянной киянкой в дальнем конце цеха? Никак, вкрапления советских ноу-хау в современный быт «Шкоды»?
Ни в коем случае, отвечают представители концерна. Рихтовка кузовных деталей – часть современной технологии, и она отражает не безалаберность рабочих, а наоборот, изнурительное внимание к деталям. Дескать, штамп не всегда дает 100-процентное попадание в форму, и идеальные поверхности выводят мастера высокой квалификации, не повреждая при этом цинковые покрытия кузовов. Так делают здесь, так делают в Германии при производстве Porsche Panamera. А если кто «забудет» поправить кузов – дефект поверхности обнаружат на выходном контроле, и мастер получит минус в свою «карму».
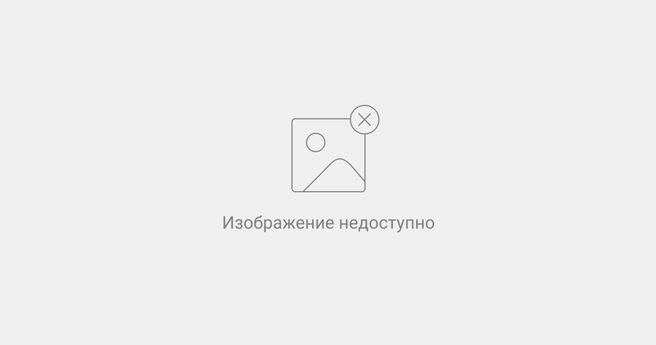
Самый современный завод Volkswagen?
От прежнего производства остались лишь несколько роботов, купленных для новой линии по производству многострадальной Volga Siber, да редкие-редкие пульты управления. В остальном цех выскребли до штукатурки и оборудовали заново, оттого он пестрит инобрендами: Siemens, Kuka, Leica, Durr...
Петр Линхард, руководитель нижегородского предприятия Volkswagen, утверждает, что это – один из самых современных заводов концерна в мире. «Заводы, как и машины, постоянно совершенствуются, так что чем позднее построено предприятие – а этот завод пущен в декабре 2012 года – тем новее и лучше оборудование».
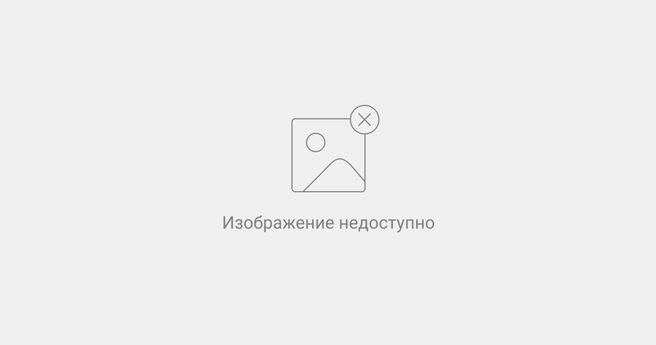
А можно пример? Пожалуйста: лазерная пайка деталей, технология ювелирной промышленности. Оборудование для пайки заметно дороже, чем для традиционной контактной сварки, зато шовчик получается – ммммм, аппетитным и ровным, как бобслейный желоб. И главное – непрерывным.
Причем в новых Skoda лазерная пайка будет вытеснять обычные методы: так, если общая длина спаиваемого шва у Yeti – 1,2 метра, то у новой Octavia, которую запустят в Нижнем Новгороде летом – 6,2 метра. В результате, количество сварных точек сокращается на 40%: с 4690 до 3338. А значит, кузов будет жестче, надежнее и, за счет меньшей металлоемкости, легче.
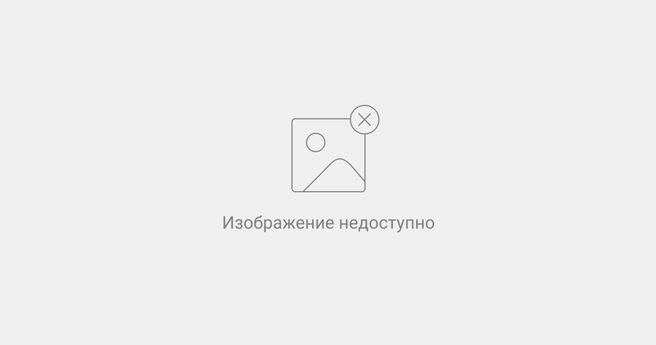
А вот специальный автомат-сварщик для точного позиционирования крупных деталей. Например, на АВТОВАЗе при сварке «Калины» боковины и пол совмещают вручную, а здесь – в автоматическом режиме без погрешностей.
Другое ноу-хау Volkswagen – воскование кузовов. Уже после окраски и частичной сборки в специальной камере все скрытые полости автомобиля заполняются воском, который через десятки форсунок закачивают в автомобиль из 16-тонной ванны. В среднем на каждую Skoda приходится по 3,5 килограмма воска, защищающего от коррозии потайные ниши: внутри арок, под полом, в лонжеронах.
В кузовном цехе работает 137 роботов, и степень автоматизации составляет 28%. Но и ручного труда много, в том числе с помощью гигантских, больше человеческого роста, сварочных клещей, с которыми рабочий выглядит ученым-маньяком. Все ручные операции максимально формализованы, чтобы снизить вероятность ошибки, тем не менее, от людей тоже зависит немало – поэтому контролируют их тут, как крепостных.
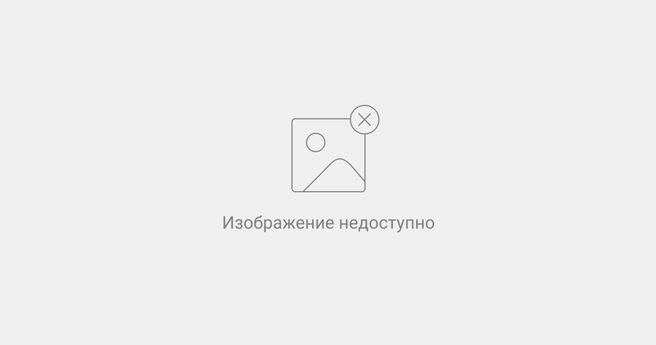
Семь раз промерь, один прокрась
Например, геометрия кузова – проще говоря, правильность его формы. На что она влияет? Да на все: на ровность зазоров, на жесткость кузова, настройку подвески и безопасность при столкновении.
Геометрию на заводе проверяют многократно, в том числе два кузова в смену снимают с конвейера и посылают на дотошный инструментальный контроль. Специальный робот с «рубиновым» щупом (для износостойкости) снимает координаты сотен точек и делает заключение о соответствии кузова или отдельной панели идеалу.
Петр Линхард хвастается: «Это еще что... Через неделю смонтируем новый оптический комплекс Leica, который будет проверять 100% кузовов на геометрическую правильность «в прямом эфире». Но вот этот, «рубиновый» измеритель все равно останется – он дает еще более точные и детальные результаты».
Вообще, к дефектам здесь относятся... толерантно. В том смысле, что само по себе появление дефекта в процессе изготовления не считается концом света. Весь вопрос в том, чтобы отловить его как можно быстрее и исправить. Закрывать глаза на недочеты – все равно что добавлять себе в еду мышьяк. Рано или поздно того... Скопытишься.
«Чем позже мы обнаружим дефект, тем дороже он нам обойдется, – говорит Петр. – Вон там, в конце цеха сборки есть зона финального контроля. Если вдруг обнаружится нарушение геометрии или какой-то непровар, когда автомобиль уже окрашен и полностью собран – машину просто «пустят на органы», разберут и утилизируют. На самом деле таких прецедентов не было – любой мелкий дефект обнаруживается на гораздо более ранних стадиях и исправляется сразу».
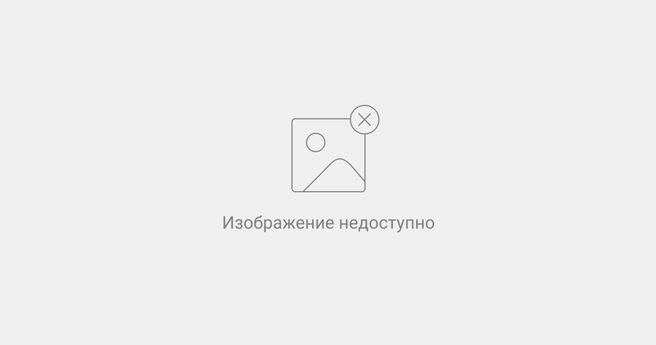
Допустим, сварщик, прежде чем соединить две детали, оценивает их на «адекватность» – если есть сомнения, деталь откладывается в сторону и вызывается специалист по дефектовке.
А вот на стене вывесили результаты теста в дождевальной камере, где кузова проверяют на герметичность. Текст гласит: «Водный тест. Количество проверенных автомобилей – 22. Вода в заднем кармане (1). Неверное нанесения пластизоля. Ответственный – окраска».
Это значит, что подтекающий кузов отправится на доработку, а мастер, который неверно нанес пластизоль, получит финансовый «пендель», а то и вовсе отправится на переобучение.
И такой контроль – повсеместный. Не только службы внутреннего контроля, но и внешний аудитор может проверить моменты затяжки болтов или снять кузов и отправить в зону контроля, а по результатам устроить «разбор полетов». Халтурить здесь попросту невыгодно: в лучшем случае проделаешь ту же самую работу два раза (второй раз – бесплатно).
Вообще, взаимоотношения «Группы ГАЗ» и концерна Volkswagen в рамках этого проекта необычны. Здесь, в Нижнем Новгороде, идет так называемая контрактная сборка. Это значит, что за технологии и контроль качества отвечает европейская сторона, а за сам производственный процесс – наша. Пока автомобиль едет по конвейеру – он еще не является ни «Шкодой», ни «Фольксвагеном», и чтобы получить этот престижный статус, нужно пройти выходной контроль. Его в специальной зоне завода выполняют специалисты Volkswagen, по сути, чужие для предприятия люди – у них даже униформа своя. С заводчанами они фактически не общаются, и результаты своих изысканий отражают не в душевной беседе «Ну что ж ты, Семен, опять лажаешь», а в виде официальных заключений. Обнаружили мелкий дефект – автомобиль на доработку и снова в зону контроля. Если дефект серьезный – вплоть до полной «утилизации». И лишь когда машина отвечает всем параметрам, она получает VIN-номер и становится товарным автомобилем.
Чтобы никто не ушел от ответственности, данные о всех рабочих, начальниках смен, технологических режимах и т.п. для каждого выпущенного автомобиля хранятся в архивах 15 лет.
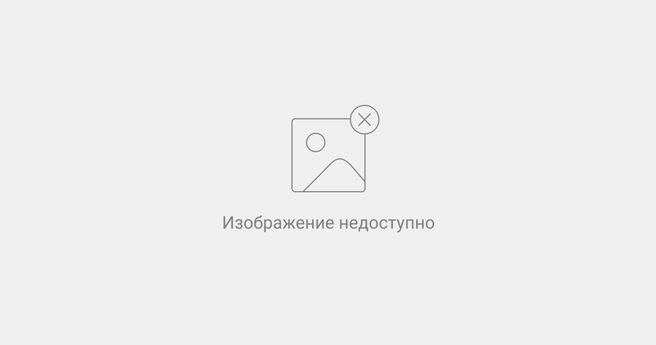
А руки-то чьи?
Знаете, что поражает на автомобильных заводах, и не только в России? Неспешность, с которой рабочие выполняют свои обязанности. Покрутили, постояли, приварили, постояли...
Это тоже фактор, работающий на качество – не загнать рабочих. В Нижнем Новгороде конвейер пока неспешный: такт длится 180 секунд. Со временем, видимо, скорость возрастет. Пока же здесь много чехов, которые руководят производством, обучают рабочих и следят за качеством. Со временем иностранцы передадут свои полномочия российским специалистам, и тогда...
Любимая гипотеза: мол, наши машины плохие, потому что у нас руки кривые. Нет, друзья, качество определяют не руки рабочих, а голова руководства. На тех же европейских заводах работает много иммигрантов из Турции, Вьетнама, а то и бывшего Союза, но работают совсем не так, как в годы распутства на ГАЗе или АВТОВАЗе.
Новые Skoda в Нижнем собирают в том числе рабочие, которые знали еще «Волги». Точный процент новичков и старожилов нам не сказали, но примерно – 50:50. Не вредит ли сотруднику предыдущий опыт постсоветского автопрома?
«Нет, – отвечает Петр Линхард. – Не важно, сколько километров швов заварил сотрудник «в прошлой жизни» – ему все равно предстоит пройти полное обучение по стандартам Volkswagen, а затем – испытательный срок на производстве».
А как бывшие «волгоделы» относятся к необходимости снова идти в учебные классы, которые здесь, в Нижнем Новгороде, просто огромные и занимают площадь более 3000 квадратных метров?
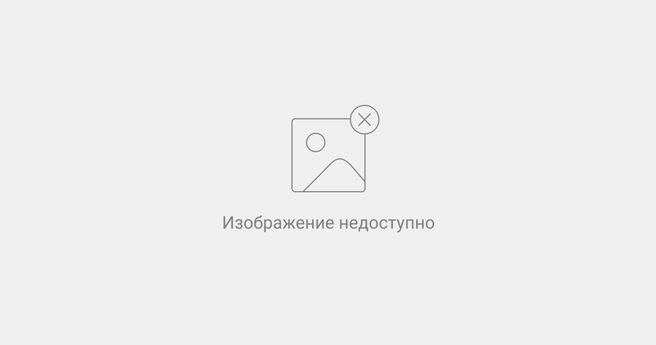
«Конечно, сначала со скепсисом – мол, что вы нас будете учить, как гайковерт держать? – отвечает руководитель учебного центра Иван Дубровин. – А потом мы показываем правильные позы, при которых снижается нагрузка на суставы, и даже бывалые удивляются: надо же, столько лет работали, мучились, а таких мелочей не знали».
Срок обучение поражает воображение: неделя в учебном центре, еще две недели на производстве. Причем, никаких специфических требований к кандидату нет – было бы желание работать и соблюдать стандарты.
Итак, три недели, и рабочий готов. Не быстро ли? «Нет, ведь его постоянно курируют и на производстве, – отвечает Иван Дубровин. – А я, когда поступил на «ГАЗ», не учился ни дня: просто вышел утром на работу и стал сварщиком. Дело не в длительности обучения, а в эффективности методики».
Методика весьма креативная. Есть, конечно, теория, но много заданий напоминает игру. Например, на учебной доске приколоты этак сотня карточек с цифрами, да все разными шрифтами – что-то вроде «капчи». Человеку нужно быстро отыскать среди них числа от 1 до 60 и перечеркнуть фломастером. Умные выстраивают в рядок и черкают оптом.
Есть, конечно, и более конкретные тренировки, например, сварщики упражняются с настоящими клещами, водители автопогрузчиков учатся грузить огромные лари на верхние этажи стеллажей, а маляры красят водой.
Некоторые задания с подвохом: например, сборщикам на конвейере дают заведомо «кривую» технологическую карту, проверяя, смогут ли они найти ошибку. Да, из человека здесь делают биоробота, но ведь и робот должен быть адекватным.
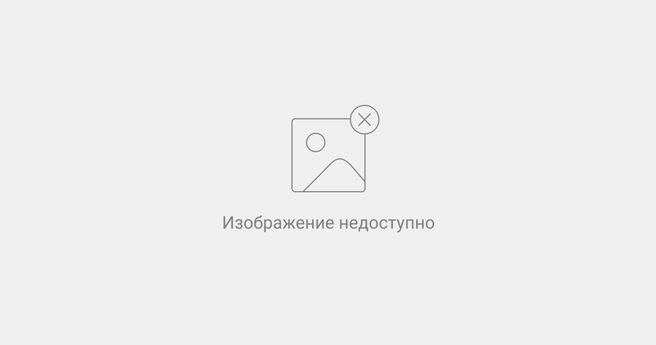
Новый «ГАЗ»
Производство собственных моделей «Волга» зачахло в 2009 году, еще через год «сдулся» амбициозный проект Siber – новая «Волга», практически идентичная Chrysler Sebring, технологию и завод по производству которого «Группа ГАЗ» купила в 2006-2007 годах. Устаревший на тот момент, построенный под вкусы американцев седан не пользовался спросом и оказался убыточным: с горем пополам, газовцам удалось выпустить около 9000 машин.
Параллельно забуксовал еще один проект «Группы ГАЗ» – производство коммерческой техники английской компанией LDV (бренд Maxus), которую отечественный гигант купил в 2006 году. Как и в случае с «Сайбером», планы были амбициозные, но дело не пошло – в том числе, из-за кризиса 2008 года.
В 2009 году к руководству Горьковским автозаводом пришел швед Бо Андерсон, человек с неоднозначной репутацией – до этого он был вице-президентом General Motors по закупкам и прослыл руководителем жестким и очень прагматичным.
То, что пугало американских поставщиков, похоже, оказалось абсолютно уместно в российских реалиях: Бо Андерсон подошел к делу сугубо рационально и, наверное, это спасло завод от коллапса легкового производства.
На заводе простаивали огромные цеха, оставшиеся от «Волг» и «Сайберов», а вместе с ними – сотни рабочих. В то же время автоконцерны, подписавшие новое соглашения о промсборке, подыскивали площадки для расширения производства до 300-350 тысяч автомобилей в год.
Проектом с «Группой ГАЗ» заинтересовался General Motors: часть цехов заняло производство полного цикла Chevrolet Aveo объемом 30 тысяч в год. Потом пришел Volkswagen с еще более серьезным проектом, рассчитанным на 110-130 тысяч автомобилей в год.
Иностранцы получили готовую инфраструктуру: цеха, транспортные магистрали, котельные. Завод смог занять тысячи рабочих, содержать цеха, платить налоги... Наш мини-опрос нижегородцев показал, что к инициативам Бо Андерсона относятся позитивно – пусть производство не свое, но все же лучше, чем полная разруха. В возможность создания своей конкурентоспособной легковушки на «ГАЗе», похоже, давно никто не верит.
Важно подчеркнуть, что завод Volkswagen хоть и находится на территории «Группы ГАЗ», все же нельзя считать совместным детищем: вся «идейная подоплека» здесь – иностранная, наши только рабочие, стены и валюта. Грубо говоря, все технологии, до последней запятой, принадлежат Volkswagen, так что в глобальном смысле на подъем российского автопрома этот проект, как и другие просборочные предприятия, не работает. С точки зрения концерна VAG, нижегородский проект – это еще один из более чем 60 заводов по всему миру, от Германии до Австралии.
Но именно это дает уверенность, что качество нижегородских Skoda и Volkswagen ничем не отличается от тех, что везут к нам из Мексики, Испании или Германии.
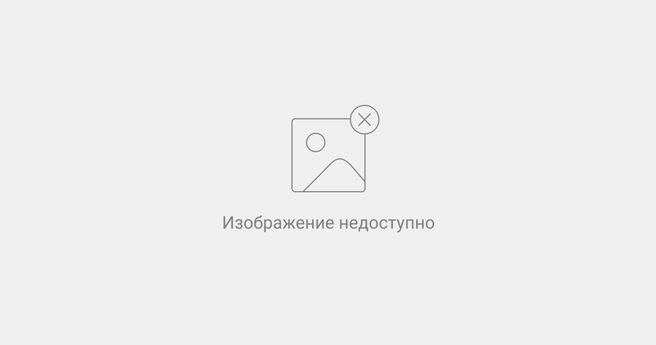
Платформа MQB
Новая Skoda Octavia, которую начнут делать в Нижнем к лету, построена на совершенно новой платформе MQB – революционном новшестве Volkswagen (ныне выпускаемые Yeti и Jetta «сидят» на платформе PQ35).
На платформе MQB Volkswagen планирует строить автомобили самых разных сегментов: от малыша Volkswagen Polo (Skoda Fabia) до семиместного кроссовера CrossBlue, размером с Toyota LandCruiser Prado.
Речь идет о глобальной унификации моделей. Компоновки моторного отсека, дверные петли, части кузова, электрооборудование и многое другое будет одинаковым от модели к модели, тогда как длина колесной базы, ширина, отделка салона и другие «осязаемые» компоненты будут разниться.
Такая унификация существенно снизила себестоимость, упростила производство и логистику. В результате, без резкого роста цены концерн смог применить в моделях большее число высокопрочных сталей, лазерную пайку и ряд других дорогих технологий. Один из результатов – легкость шасси: к примеру, новая Skoda Octavia в базовой версии весит 1150 кг, то есть примерно на 150-300 кг легче «среднерыночного» значения для класса.
«Сожительство» двух платформ – PQ35 и MQB – в Нижнем Новгороде не создает технических проблем: производственные линии настроены гибко и могут выпускать разные машины вперемешку. Когда на очередной пост приезжает новый кузов, рабочий или робот считают штрих-код и оборудование перенастраивается под соответствующую модель.
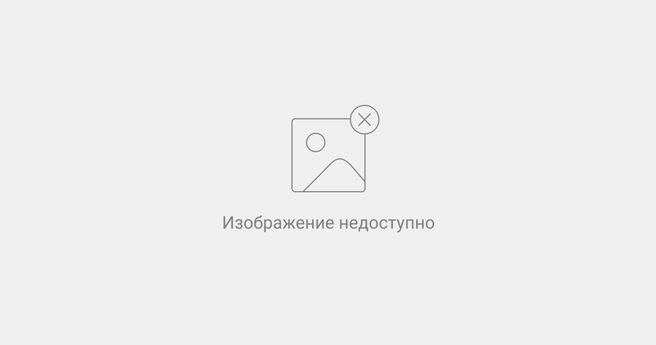
Заводы Volkswagen/Skoda в России
Фото: Фото автора и Андрея ВИННИКОВА